-
Automatic Filling Machines
-
Water Bottle Filling Machine
-
Carbonated Soft Drink Filling Machine
-
Juice Filling Machine
-
Automatic Canning Machine
-
Beer Filling Machine
-
Glass Bottle Filling Machine
-
Reverse Osmosis Water Treatment System
-
Bottle Labeling Machine
-
Shrink Wrapping Machine
-
High Speed Shrink Wrapping Machine
-
Beverage Processing System
-
Date Printer Machine
-
Blowing Mould Machine
OPP Oval Bottle Labeling Machine 24000 Cph Hot Melt Labeling Machine
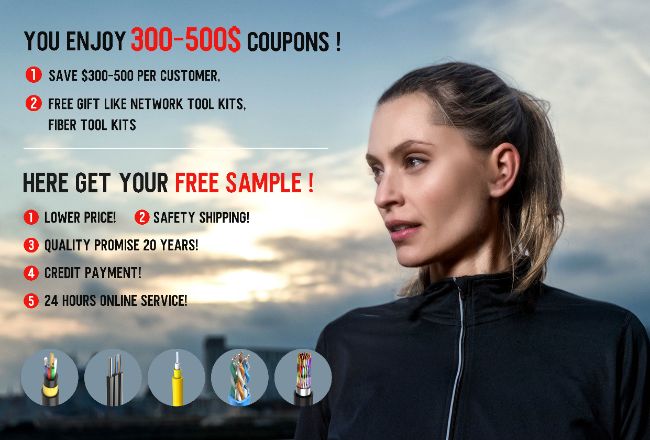
Contact me for free samples and coupons.
Whatsapp:0086 18588475571
Wechat: 0086 18588475571
Skype: sales10@aixton.com
If you have any concern, we provide 24-hour online help.
xSpeed | Up To 24000 Bottles Per Hour | Labeling Accuracy | ±0.5mm |
---|---|---|---|
Bottle Type | Plastic Bottle, Glass Bottle, Metal Can | Bottle Size | Out Diameterφ40mm~φ120mm,height30mm~200mm(can Be Customized) |
Label Material | OPP/ Pearl Film/Composite Paper | Label Size | (bottom)Height40~200mm,Length120~376mm |
Label Thickness | 0.04-0.05mm | Power | 10KW |
Air Consumption | 0.4Mpa | Dimension(L×W×H) | Approx 5000×1600×2000mm(including The Length Of Conveyor Belt) |
Machine Weight | Approx.2000kg | ||
Highlight | OPP Oval Bottle Labeling Machine,24000 Cph Hot Melt Labeling Machine,Bottle Labeling Machine 24000 cph |
Automatic high speed rotary hot melt adhesive labeling machine for opp label hot glue
The Roll-Fed labelling station is equipped with two IT independent reel stands, complete with film tension control device. During its unwinding, the film is controlled by a continuous, automatic correcting system of its vertical position [web tracker]. The film feeding roller is controlled by a servo-motor which adjusts the film feeding speed in accordance with the labels pitch (spot or other reference). The label is cut onto a drum provided with rotating blade which interferes with a static blade. The fine adjustment of the alignment of the two blades, necessary for a correct cutting and a long life of the blades, is simple and reliable. The transfer of the label from the cutting drum to the container is carried out by means of an aluminium vacuum drum.There is no slipping between the cut label and the vacuum drum: the machine functioning does not depend on the variation of the parameters related to the label material and to the upper finishing of the vacuum drum. The label process is therefore less critical. The Hot-Melt glue is spread on one edge of the label and on the overlap by means of a glue roller made of stainless steel, provided with a high precision and finely knurled cylindrical surface permitting a minimum consumption of glue. The labelling station position may be adjusted either vertically or horizontally, in order to allow the handling of containers of different diameters and the application of labels at different heights.
The Roll-Fed labelling station is equipped with two IT independent reel stands, complete with film tension control device. During its unwinding, the film is controlled by a continuous, automatic correcting system of its vertical position [web tracker]. The film feeding roller is controlled by a servo-motor which adjusts the film feeding speed in accordance with the labels pitch (spot or other reference). The label is cut onto a drum provided with rotating blade which interferes with a static blade. The fine adjustment of the alignment of the two blades, necessary for a correct cutting and a long life of the blades, is simple and reliable. The transfer of the label from the cutting drum to the container is carried out by means of an aluminium vacuum drum.There is no slipping between the cut label and the vacuum drum: the machine functioning does not depend on the variation of the parameters related to the label material and to the upper finishing of the vacuum drum. The label process is therefore less critical. The Hot-Melt glue is spread on one edge of the label and on the overlap by means of a glue roller made of stainless steel, provided with a high precision and finely knurled cylindrical surface permitting a minimum consumption of glue. The labelling station position may be adjusted either vertically or horizontally, in order to allow the handling of containers of different diameters and the application of labels at different heights.
Flexibility
*High performances with a wide range of label materials (OPP, PET, PVC, OPS, PAPER).
* Non stop production; • Easy to operate.
*Low TCO (Total Cost of Ownership).
* Plug & Play technology (easy installation into the line guaranteed by a compact machine layout).
*User friendly.
Efficiency, reliability and accuracy
*Highest speed with only 1 labelling station.
* Low cost for change and spare parts.
Sustainability
*A labeller which works with OPP wrap-around labels provides the most cost-effective solution for customers with high volume and high speed labelling requirements.
*Our labellers have been designed to handle lighter weight containers and lighter weight labels.
*Low energy consumption.